World-First Mango Auto Harvester Targets Labour Force Issues
Description
CQUniversity's world-first mango auto harvester is turning industry heads with the promise of targeting labour force issues. At three metres tall, the third iteration of the prototype moves a platform of arms up and down, while sensors scan the mango orchard for fruit. Once identified, mechanical arms reach out to grab, rotate, retract and drop.
Partners
This project is being delivered through Hort Innovation with support from the Rural Research and Development for Profit program of the Australian Government Department of Agriculture, Water and the Environment, and mango supply groups Pinata, Manbulloo, and Perfection Fresh.
Impact
The harvester, which is part of an integrated system that includes crop forecast, targets the labour force issues that currently limit the industry – in terms of both labour availability and the safety issues of harvesting in the summer heat and working with a fruit that spurts an acidic sap.
Professor Kerry Walsh
For many Australian mango farmers across the horticultural sector, COVID-19 presented many additional disruptions to the harvesting season, on top of pre-existing labour force issues.
Harvesting jobs are transient and picking in 40-degree heat, while working at heights and dealing with acidic sap, is not for the faint-hearted.
Over the years, the harvest labour force has shifted from domestic to international, however COVID-19 has proved that to be a risky business model. That is why CQUniversity's world-first mango auto harvester is turning heads in the sector.
The prototype, developed by Professor Kerry Walsh and his research team, has achieved a 75 per cent efficiency rate in automatically identifying and picking fruit in view.
At three metres tall, the third iteration of the prototype moves a platform vertically, while sensors scan the mango orchard for fruit. Once identified, mechanical arms reach out to grab, rotate, retract and drop.
'The technologies that underpin the auto harvester, like machine vision, have become of age, and as a result, the cost has dropped. It's time to apply.'
'But there is a trade-off between technology complexity and cost. We target a sweet spot of harvest efficiency and technology simplicity and reliability'.
Professor Walsh says the prototype harvester will help to mitigate the current labour force issues by providing mango farmers with an effective automated harvesting process.
'At present, farmers use 'harvest aid' platforms that travel through the mango orchard. These can either be self-propelled with a driver or towed with a tractor,' he says.
'Up to eight pickers work around the platform. Workers have approximately three seconds between picking the fruit and placing it in an alkaline solution on the harvest aid, before the acidic sap that spurts from the fruit when picked can burn the skin of the fruit.
'Our prototype is set to automate the pick and place process.
'It will integrate with a harvest aid and is set to reduce farm harvest labour needs while driving consumer demand by ensuring a top-quality eating experience every time.
Professor Walsh says the sector's interest in the mango auto harvester is a sign that automation is here to stay. 'People are adapting and they know they have to. What was commercially viable five years ago, is not now,' he says.
'The packhouse has become automated. Previously, the fruit was hand-sorted and hand-packed. Now, you will see conveyer lines, bin loaders and pallet wrappers. Similarly, the rest of the supply chain is automated, with the use of forklifts and other aids, but every mango is still hand-picked from the tree. It's time to take packhouse technology into the orchard.'
Already produce such as potatoes and nuts are mechanically harvested, but soft fruits are more challenging. Also, different soft fruit types have different harvesting techniques, so it is not one size fits all for harvesting automation.'
'There are several companies entering the apple robotic harvesting space,' he says. 'However, if you are a farmer waiting for this technology to be adapted or changed to suit a mango harvest, you will be waiting a long time. That's why we have entered the space.'
'The issue is very Australian – McKay invented a combined wheat harvester in the 1850s because the labour force had disappeared into the gold rushes. While the Toft brothers developed a sugar cane harvester because labour was scarce during WW2.'
Professor Walsh said he had received comments that the technology would decrease employment. 'But just like the industrial revolution in general, you decrease the number of manual jobs in one area but create a different set of jobs.'
'For example, auto-harvesting technology will require technical, maintenance and operating support, across its life cycle. In increasing productivity, it should also allow more production, and expand exports'
CQUniversity researchers are now working to take their auto-harvest technologies to commercial-ready deployment. This season's fieldwork starts in September at NT Lands in Katherine, NT.
'We are negotiating with a commercial partner to deliver a product into use,' Professor Walsh says.
The CQUniversity group has previously delivered near-infrared spectroscopy (NIRS) measurement system into the industry, where it is now used to assess the eating quality of mangos and predict the ideal harvest time.
This research was funded by the Australian Government Department of Agriculture and Water Resources as part of its Rural R&D for Profit program through Hort Innovation, with support from CQUniversity, project ST19009.
Find out more about the clever collaborations between Australia's universities and businesses.
Connect with CQUniversity
At CQUniversity we know the value of our connections locally and around the world. Our partnerships help us create opportunities, deliver solutions and change lives. From time to time, we share our Connections Count update where we share our highlights, including research impact stories like the ones below. Sign up to become one of our valued connections.
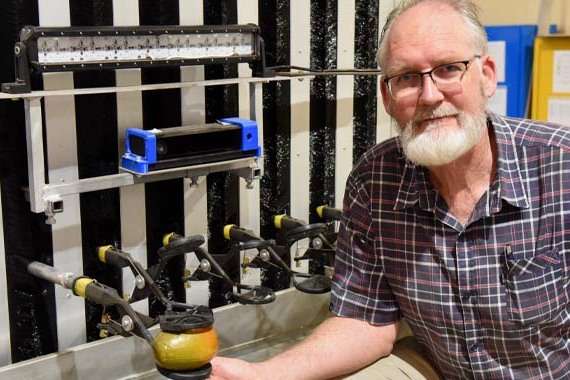